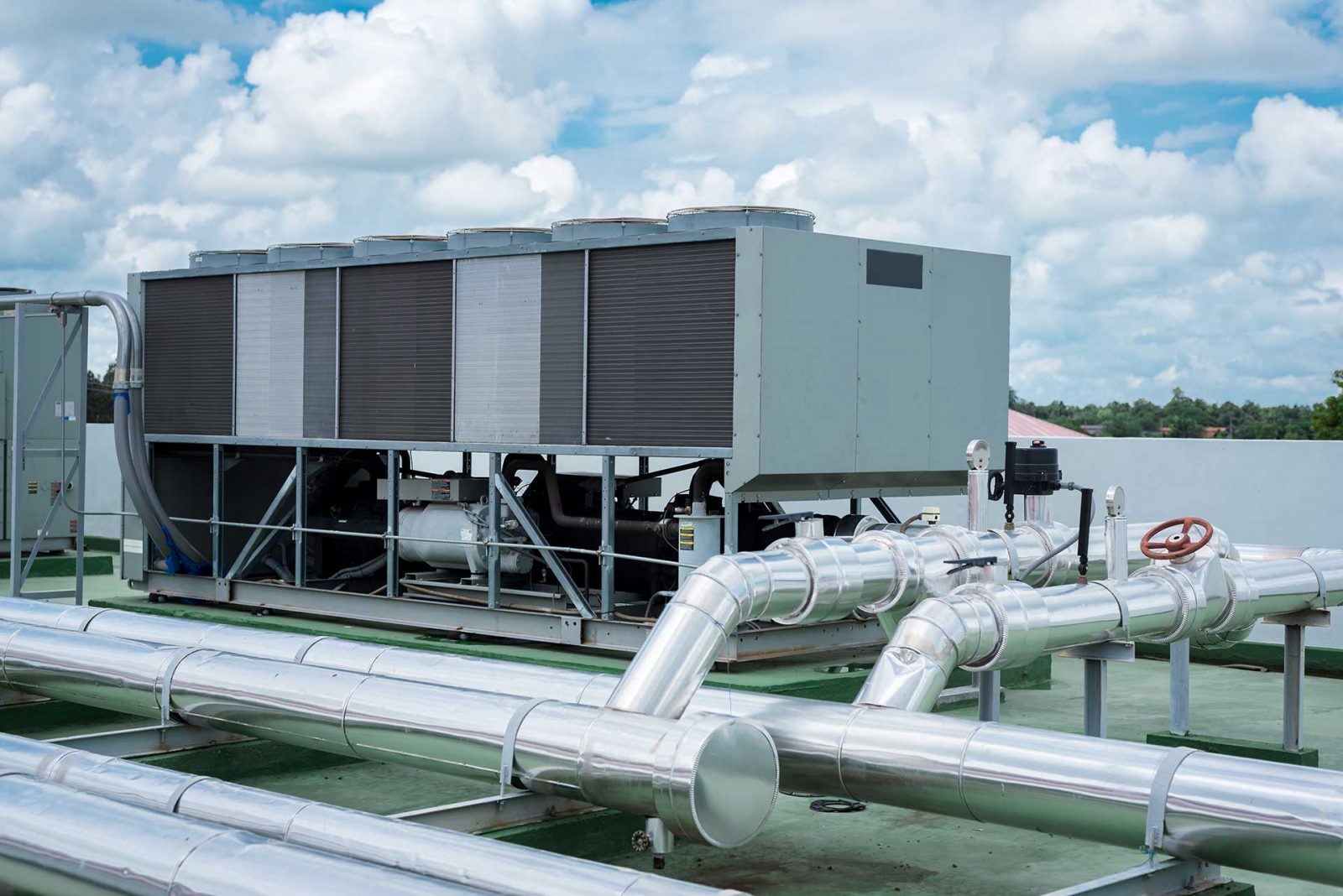
Em indústrias, há processos de troca térmica ocorrendo a todo instante, seja para fins de aquecer uma corrente de processo ou para resfriar. Apesar dessa operação poder ser feita sob diversas formas (uso de micro-ondas, irradiação, resistência elétrica, fornalhas, etc.), o mais comum para sistemas que exigem alta carga térmica é o emprego de utilidades, as quais são correntes de um fluido – muito comumente água ou vapor – que está indiretamente em contato com o material que se pretende aquecer/esfriar. Isso ocorre pela transferência de calor do meio mais quente para o mais frio, através das paredes da tubulação/equipamento que separam cada material.
De maneira geral, para aquecimento de correntes, utiliza-se vapor saturado sob altas pressões, por ser um material relativamente barato e extensamente conhecido. Já para resfriamento, depende muito da faixa de temperatura que se deseja atingir, sendo que para temperaturas ligeiramente baixas (cerca de 60 a 70ºC), pode ser utilizado água de torres de resfriamento, a qual é uma água que é resfriada ao entrar em contato com ar atmosférico.
Entretanto, para poder resfriar sistemas cuja temperatura objetivo é próxima da temperatura ambiente ou abaixo, o uso de água oriunda de torres de resfriamento se mostra inadequado, sendo limitada apenas para redução de temperaturas até cerca de 20ºC acima da temperatura ambiente. O uso de fluidos refrigerantes é uma alternativa nesses casos, mas devido ao seu alto custo de aquisição e operação, esse material é reservado para fins mais exigentes e/ou lucrativos, como resfriamento de uma corrente de produto para sua purificação ou promover uma reação química. Por conta desses fatores, uma solução mais indicada para montar um sistema de refrigeração para necessidades mais moderadas, mas que torres de resfriamento não conseguem atender, é o uso de Chillers e Sistemas de Água Gelada.
Os Chillers correspondem a um equipamento que, por meio de princípios de compressão e descompressão, conseguem gerar uma utilidade com temperatura abaixo da ambiente, o que possibilita resfriar correntes de maneira mais eficiente e até temperaturas menores. Quando esse equipamento é utilizado para produzir água de utilidade, chama-se esse processo de “sistema de água gelada”, o qual pode ser utilizado para diversas aplicações de resfriamento de correntes, como na indústria metalúrgica ou farmacêutica, porém o Chiller também é utilizado para refrigeração de ar ambiente, muito comum em shoppings centers e aeroportos.
De maneira geral, o sistema de refrigeração industrial consiste em um ciclo fechado por onde um fluido refrigerante passa continuamente em um compressor, um condensador, uma válvula de expansão e uma evaporadora. Abaixo, a forma de operação de cada etapa será brevemente explicada para melhor compreensão do funcionamento do equipamento:
Compressor: neste equipamento, o fluido refrigerante tem sua pressão elevada, de forma que sua temperatura também aumenta por conta da dependência que essas propriedades tem entre si (essa propriedade termodinâmica é conhecida como “Lei dos gases” e mostra como o volume, pressão e temperatura de fluido gasosos são intrinsecamente dependente entre si).
Condensador: esta etapa consiste em uma troca térmica entre o fluido aquecido e comprimido com um fluido mais frio, como água de torre de resfriamento, de forma que o refrigerante terá uma temperatura mais amena, porém sob pressão alta. Aqui, parte do fluido pode condensar, motivo pelo qual possui esse nome.
Válvula de expansão: após a condensação, a pressão do fluido é drasticamente reduzida, causando o efeito contrário da compressão, isto é, a temperatura do fluido cai. Isso possibilita que o fluido finalmente possa agir como refrigerante de outra corrente e alcançar seu objetivo principal.
Evaporador: esse equipamento é simplesmente onde ocorre a troca térmica entre o fluido refrigerante e a corrente que se deseja resfriar (água gelada ou ar). O fluido volta a ter uma temperatura amena e é levado até o compressor, onde o ciclo se reinicia.
Esse sistema é uma ótima opção para produzir uma utilidade que irá atuar em refrigerações mais amenas, onde não há necessidade que a troca térmica da linha de processo seja diretamente com o fluido refrigerante. Entretanto, para o funcionamento adequado da operação, é preciso haver uma manutenção regular do sistema de água gelada, pois muitas vezes esta se encontra num ciclo fechado e, portanto, possibilita o desenvolvimento de alguns problemas que afetam o desempenho do equipamento.
Um dos problemas mais comuns se tratando não apenas de água gelada, mas de serviços de água num todo, é o surgimento de incrustações, que é a formação de camadas de sólidos aderidos nas superfícies de tubulações e equipamentos. Isso ocorre quando há flutuações de temperatura e/ou pH em uma água que possua sais dissolvidos, comumente chama de “água dura”, de forma que a cristalização desses compostos seja promovida.
As duas principais consequência desse fenômeno são: a perda de eficiência de troca térmica, pois a espessura das paredes entre fluidos será maior que a projetada e, portanto, será necessária uma área de troca térmica maior para atingir um mesmo objetivo de temperatura final; e o entupimento de tubulações por conta do acúmulo de sólidos obstruir a passagem d’água. Uma solução para esse problema é a dosagem de produtos químicos, chamados de “sequestrantes de dureza”, que inibem a ação prejudicial desses sais, além da realização de purgas regulares para que haja redução das concentrações desses sais.
Outro problema atrelado a sistemas de água gelada é corrosão, causado por gradientes de concentração ou pH que são favoráveis à reação de oxidação do ferro. Isso fragiliza a integridade das tubulações, causando vazamentos e até perda total de linhas. Para evitar isso, o uso de agentes químicos inibidores de corrosão é uma solução muitas vezes empregadas, por ser uma medida simples e relativamente barata.
Realizando esse controle, tratamento e monitoramento da água, os sistemas de água gelada podem operar com muita tranquilidade, sem oferecer riscos de paradas não programadas às plantas industriais.